The fabrication of springs is a process that necessitates precision and careful selection of materials. Typically, a high-tensile steel wire is molded into the desired shape, as this material balances elasticity and strength effectively. During this process, springs are subject to significant mechanical stress, necessitating a coating that can withstand friction, environmental factors, and corrosion over time. Surface treatments for springs must therefore adhere to stringent criteria, including resistance to wear and the ability to maintain spring properties throughout their lifecycle. Given these stringent requirements, the industry constantly seeks innovations in coatings and treatments that can extend the life of spring mechanisms in various applications.
The Role of Coatings in Enhancing Spring Performance
Coatings provide a multifaceted benefit to springs; they extend their useful life by protecting against the elements that can weaken or degrade them over time. Among these benefits, corrosion resistance stands at the forefront. Coatings serve as a barrier, preventing chemical reactions between the spring material and corrosive substances present in the environment. This can dramatically prolong the lifespan of springs, especially in industries where exposure to harsh elements is a daily challenge. Springs functioning within maritime, automotive, or industrial machinery settings often encounter a variety of corrosive agents such as saltwater, chemicals, and oxidizing agents, all of which can lead to rapid deterioration of unprotected metals.
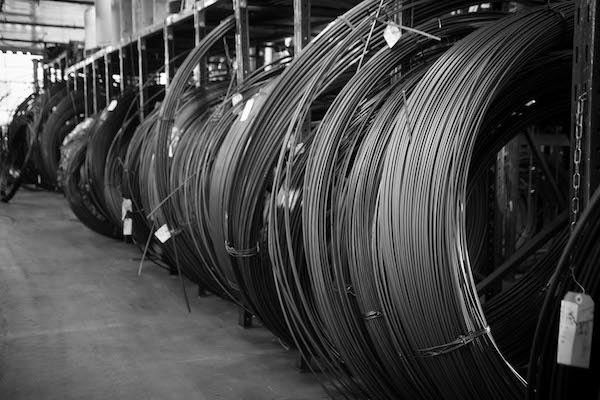
Aside from thwarting corrosion, coatings contribute significantly to the wear protection of springs. In applications where there is constant motion – such as in valves, switches, and suspension systems – the repetitive friction can wear down even the most robust materials. Coatings act to minimize this wear, allowing the spring to maintain its structural integrity and load-bearing capacity over time. By creating a harder surface, some coatings can substantially increase the spring’s resistance to surface wear and abrasion.
The relationship between surface hardness and spring performance is undeniable. Harder surfaces are less susceptible to deformation and can better endure the cyclical stresses that springs endure. This not only promotes longevity but also maintains the precise force and deflection characteristics required for the spring to function correctly. A spring that maintains its shape and strength is a reliable component in any mechanism.
Lastly, an often overlooked aspect of coatings is their environmental impact. Selection of coating materials and processes must factor in the ecological footprints they leave behind. Regulations continue to evolve, pushing manufacturers towards the adoption of more environmentally friendly solutions without compromising performance. Advanced coatings are developed to address these concerns, offering protection while being mindful of waste, emissions, and toxicity.
- What types of coatings offer the ideal balance between environmental considerations and performance enhancement?
- How might the selection of a coating impact not only the spring’s lifespan but also its operational capabilities?
Coating Materials for Maximum Protection
Springs operate in diverse environments, continuously exposed to stress, friction, corrosion, and variable temperatures. Maximum protection is achieved through the application of high-performance coatings. Each material offers distinctive benefits tailored to specific operational requirements.
Epoxy
The robust protective qualities of epoxy coatings derive from its chemical composition, which provides hard and durable finishes. These coatings function well in environments where resistance against corrosive substances and abrasion is required. The cross-linked structure of cured epoxy endows springs with longevity and resilience against physical damage during operation.
Polyurethane
Polyurethane coatings leverage their inherent flexibility and impact resistance to safeguard springs. Their unique formulation enhances the spring’s ability to absorb energy and resist forces without deforming. Polyurethane’s versatility proves beneficial in applications involving frequent or sudden movements, where it mitigates the potential for wear and tear.
Acrylic
Acrylic coatings are distinguished by excellent weatherability, making them the preferred choice in outdoor or variable climate conditions. Their capacity to withstand UV radiation without degrading keeps the spring’s surface intact over prolonged exposure to sunlight, preserving both functionality and appearance.
- Epoxy offers unmatched hardness and chemical resistance.
- Polyurethane excels in flexibility and absorbs impacts effectively.
- Acrylic provides superior protection against environmental elements.
Optimizing Spring Performance with Tailored Application Methods
Spraying
When uniformity and speed are the goals, spraying stands out as the method of choice for coating springs. By engaging this technique, manufacturers ensure even coverage across the spring’s surface. Precision-controlled equipment atomizes the coating material, facilitating a consistent and efficient application process which minimizes wastage and maximizes adhesion.
Dipping
Complex geometries necessitate thorough application techniques, and dipping fulfills this requirement. Springs are immersed fully in the coating substance, allowing the material to envelop and bond to every contour. This method excels in reaching recesses and crevices that other approaches might overlook, offering complete surface protection.
Brushing
While automated methods excel in uniformity and speed, brushing caters to the nuanced needs of specific projects. For spot applications or touch-ups, brushing provides the precision required. Its direct approach caters to a manual control that sometimes proves indispensable, especially during the final stages of the coating process or when dealing with intricate spring designs.
The Crucial Role of Pretreatment and Cleaning
Surface pretreatment stands as a foundational step in ensuring coating adhesion and longevity on springs. Removing oils, dirt, oxides, and other contaminants from the spring surface is a prerequisite for successful coating application. This process directly influences how well the coating will bond to the surface, which in turn affects the coated product’s durability and resistance to environmental factors.
Recommended Cleaning Processes before Coating Application
Effective cleaning processes may vary, but common methods include:
- Solvent cleaning, which dissolves grease and oils.
- Alkaline cleaning, often in combination with ultrasonic waves for deeper contaminant removal.
- Acid cleaning, primarily for rust and scale removal.
- Abrasive blasting, which simultaneously cleans and roughens the surface for better adhesion.
Detailed evaluations of the spring material and contaminants present determine the exact cleaning protocol. Uniformity in cleaning ensures consistent coating performance across large batches. Upon completion, this sequence transitions seamlessly into the application of protective coatings, now poised for maximum effectiveness.
Ensuring Excellence through Performance Testing and Quality Control
Performance testing and quality control stand at the forefront of delivering exceptional spring coatings and surface treatments. Through rigorous evaluation, the resilience of a coating against various stressors is verified. Tests such as the salt spray method expose the coating to corrosive environments to measure its corrosion resistance. Similarly, cyclic loading tests simulate the operational stress on springs to evaluate the coating’s fatigue resistance.
In addition to testing, stringent quality control ensures product consistency and reliability. This involves continuous monitoring of the coating process parameters and frequent inspection of the coated springs. Procedures are in place to regulate the thickness, adhesion, and overall uniformity of the coating. Non-destructive testing techniques, including magnetic induction and eddy current methods, facilitate the detection of defects without damaging the spring coating. Each step of the process adheres to predefined standards to assure customers that the final product will perform as expected without premature failure.
- Accelerated weathering tests predict long-term performance in varying climatic conditions.
- Hardness tests assess the ability of the coating to resist surface deformation.
- Scratch tests determine the coating’s resistance to abrasion and surface wear.
Quality control measures are not optional but are integral to every step of the manufacturing and application process. Adherence to protocols ensures every batch of springs meets or exceeds industry quality benchmarks. This systematic approach to testing and quality control mitigates the risk of coatings failing in service, thus safeguarding against costly downtime or failures in critical applications.
Adhering to Industry Standards and Regulations
Compliance with regulatory requirements for spring coatings and surface treatments ensures product safety and broader market access. Numerous standards lay out the parameters for spring coatings within various industries. For example, the ASTM B117 standard prescribes the practice for operating salt spray (fog) apparatus, relevant to testing the corrosion resistance of coatings. Similarly, ISO 9227 provides guidelines for the same purpose but through different corrosion test conditions.
Additionally, the automotive sector often references ISO/TS 16949, incorporating specific demands for the quality of surface treatments. The aerospace industry adheres to standards like ASTM E1417, which governs the liquid penetrant testing for non-porous metals, a method often used to detect surface discontinuities such as cracks that could compromise a coated spring’s integrity. In the realm of medical devices, compliance with ISO 13485 is mandatory, addressing the quality management systems for medical device manufacturing, including the surface treatment processes.
The presence of these standards mandates that manufacturers not only comply with internationally recognized procedures but also keep abreast of regional and national regulations that might impact the use of certain materials or processes. Achieving and maintaining compliance can require manufacturers to undertake regular audits, certifications, and documentation, laying out how their coating processes meet or exceed the relevant standards.
This adherence to regulatory frameworks not only protects users by ensuring a reliable level of quality and safety but also positions a business advantage. Manufacturers with an established reputation for compliance can more easily distribute their products in global markets and attract partnerships with companies demanding a high standard of quality assurance in their supply chains.
Innovations in Coating Technologies for Springs
Recent advancements in coating technologies have significantly expanded the capabilities and lifespans of springs in various applications. Nano-coating techniques now enable the application of extremely thin films, which provide superior corrosion resistance and reduced friction without compromising the mechanical functionality of springs. This nanometer-scale engineering endows springs with improved surface characteristics and can extend their operational life, particularly in demanding environments.
Smart coatings represent another promising development, whereby the coating materials can actively respond to environmental changes. For example, certain smart coatings are designed to heal minor abrasions or scratches that occur during use, thereby maintaining a spring’s protective integrity over time. The integration of sensors into smart coatings also allows for real-time monitoring of the spring’s condition, which aids in predictive maintenance and reduces potential downtime.
Advancements in self-lubricating coatings have streamlined functionality for springs. These coatings eliminate the need for external lubrication, thereby reducing maintenance requirements and improving performance in environments where traditional lubricants would be unsuitable.
Looking forward, emerging innovations in coatings focus on sustainability, aiming to reduce environmental impact while maintaining performance. Research into bio-based coating materials as alternatives to traditional petrochemical-derived coatings may provide more eco-friendly options that still meet the stringent requirements of spring functionality.
The use of advanced polymers and composite materials for coatings is also anticipated to rise. These next-generation materials offer enhanced properties, such as increased thermal stability and improved wear resistance, which are particularly advantageous for springs exposed to extreme conditions or high cycle fatigue.
- The deployment of nano-coatings enhances corrosion resistance and reduces friction.
- Smart coatings that self-repair and monitor spring health are advancing predictive maintenance strategies.
- Self-lubricating coatings provide maintenance-free operation under various conditions.
- Research into bio-based and advanced polymer coatings is driving sustainability and performance in new spring applications.
As the spring manufacturing industry continues to evolve, these innovative coating technologies are not just enhancing the performance of springs; they are shifting the paradigm of what is possible, offering manufacturers and end-users alike unprecedented levels of efficiency, reliability, and functionality.
Maximizing Value: The Economics of Spring Coatings
Utilizing proper coatings for springs translates to significant long-term savings and a more favorable return on investment (ROI). A more durable coating extends the lifespan of springs, thereby reducing the frequency and associated costs of replacement. In applications where spring failure can lead to expensive downtime or hazardous situations, the economic benefit of a robust coating becomes pronounced.
Consider, for instance, a case study involving automotive suspension springs. An upgrade to a high-performance coating material trimmed down the need for warranty repairs and decreased the corrosion rate. These adjustments resulted in cost savings in warranty repair alone, which, in turn, reflected a positive impact on the automotive company’s ROI. Such tangible benefits help build the case for investing in advanced coatings despite apparent initial cost increases.
Examples Illustrating Cost-Efficiency
In the energy sector, downhole springs used in drilling operations benefited from specialized coatings. These coatings improved their resistance to extreme environmental conditions. This enhancement in durability prevented frequent tool failures and costly interruptions during drilling operations-a financial advantage that soon outweighed the upfront costs of the more sophisticated coatings.
Another example is seen in the electronics industry. Springs coated with materials that prevent electrical arcing exhibited fewer failures in critical components. Replacing a spring in such applications involves not only the cost of the physical part but also the cost of labor and potential damage to sensitive electronics. By using coatings that ensure the long-term functionality of springs, electronic manufacturers have sidestepped serious financial drains.
Assessment of ROI further involves factoring in the energy and resource consumption rates during the manufacturing process. Coatings that can be applied in a single step or at lower temperatures consume less energy and require fewer resources, leading to a directly calculable reduction in manufacturing costs. These cost reductions can be directly linked to a leaner manufacturing process and a healthier bottom line.
Longevity and Maintenance: The Big Picture
Dedicated maintenance regimes align closely with the durability of spring coatings. Schedules for maintenance activities hinge on the properties of the selected surface treatment. Coatings designed to resist wear, corrosion, and environmental factors directly influence the frequency and type of maintenance required. Conversely, routine inspections and care extend the lifetime of these coatings, sustaining the spring’s performance capabilities.
Maintenance and Durability
Applying a coating to a spring increases its lifespan by creating a barrier against detrimental elements. These protective layers, subject to the rigors of their operational environment, dictate the maintenance necessary to preserve spring function. For instance, springs employed in high-corrosion environments may be treated with zinc or epoxy coatings necessitating regular checks for signs of coating breakdown such as cracking or flaking, enabling timely remedial action.
Customization and Specialty Coatings
Diversified operational demands call for customized coating solutions. Choice of treatment varies from thermally sprayed ceramics for heat resistance to electroless nickel plating for smoothness and uniformity, thereby addressing unique challenges. By tailoring coatings to specific applications, the maintenance needs are also precisely defined, streamlining maintenance protocols and reducing unforeseen service interruptions.
- Durability – Specialty coatings are tailored to provide resilience in unique environmental conditions, translating to less frequent need for maintenance or replacement.
- Maintenance Optimization – Employing the correct coatings can minimize downtime and maintenance expenses by reducing wear and degradation over the spring’s service life.
Understanding the synergy between maintenance and customized spring coatings not only ensures peak performance but also maximizes the return on investment. Springs treated with appropriate coatings can consistently deliver the necessary function, even in the most challenging applications, placing them squarely at the intersection of peak efficiency and cost effectiveness.
Dealing with Extreme Conditions
Surface treatments and coatings for springs offer tailored solutions for environments that present extreme thermal and chemical challenges. Specific coatings ensure that springs can withstand high temperatures and resist degradation from chemical exposure. As applications become more demanding, these specialty coatings stand at the forefront, delivering consistent performance in the harshest of conditions.
Thermal and Chemical Resistance
Developments in chemistry and materials science have led to the creation of coating substances capable of protecting springs against thermal stress and chemical corrosion. For instance, epoxy coatings are employed for their formidable chemical resistance, while silicone-based coatings combat high-heat scenarios effectively. Springs treated with these materials maintain their integrity and functionality far longer than untreated counterparts when exposed to such extremes.
Zinc and Other Protective Finishes
Zinc coatings, applied through galvanizing or electrogalvanizing, provide a dual benefit for steel springs: enhancing both their corrosion resistance and their visual appeal. This metal finish acts as a sacrificial layer, corroding over time to protect the underlying steel from oxidizing. In addition to Zinc, finishes like phosphate coatings impart a layer of protection that inhibits rust formation and improves adhesion for subsequent painting processes, thus combining aesthetic qualities with durable performance.
- Specialty coatings render springs impervious to thermal degradation, maintaining operational strength in elevated temperatures.
- Chemically resistant coatings preserve spring functionality upon exposure to harmful substances, reducing the chance of material breakdown.
- Zinc finishes safeguard against corrosive forces, extending the spring’s useful life while maintaining its appearance.
- Additional coatings like phosphate increase adherence properties, permitting further treatment and enhancing overall resilience.
Precoating Essentials: Surface Preparation Techniques
For any coating to adhere properly to a spring and perform as expected, comprehensive surface preparation is required. Various preparation techniques exist, each tailored to different coating types, ranging from chemical treatments to mechanical processes.
Surface Preparation Techniques
- Cleaning: All surfaces must be free from contaminants such as oil, dirt, and oxide layers. Methods such as solvent cleaning, ultrasonic baths or vapor degreasing are employed to achieve a clean surface ready for coating.
- Blasting: Abrasive media blasting is used to create a profile on the metal surface that enhances the mechanical adhesion of the coating. Glass beads, aluminum oxide, or other media may be selected based on the material of the spring and the end-use requirements.
- Phosphating: A chemical conversion process that forms a layer of phosphate crystals on the surface, providing excellent paint adhesion and corrosion resistance. This is often used before the application of a primer or powder coating.
- Acid Etching: In this process, an acid is utilized to etch the surface of the metal to remove any mill scale and improve coating adhesion. It is often a precursor to galvanization or other electroplating processes.
- Zinc Plating: It involves the deposition of a thin layer of zinc on the steel’s surface to provide corrosion resistance. This technique also improves the bond strength of subsequent coatings.
- Anodizing: Applied to aluminum springs, this electrochemical process thickens the oxide layer on the surface, enhancing natural corrosion resistance and providing a better foundation for paint and other coatings.
- Surface Roughening: In situations where mechanical adhesion is crucial, the surface roughness is increased to facilitate a stronger grip for the coating. Laser texturing or peening are among the advanced techniques used for this purpose.
Each technique impacts the substrate differently and therefore must be chosen based on the type of coating selected, the environment where the spring will function, and the expected service life of the product.
Forging the Future of Spring Performance: A Final Reflection
Manufacturers recognize that the synergy between safeguards such as coatings and surface treatments deeply embeds itself in the lifespan and functionality of all types of springs. By leveraging advanced coating materials and state-of-the-art application methods, these springs enjoy amplified protection against environmental threats and mechanical stresses.
The adaptation of treatment processes before application enriches adherence and effectiveness. Furthermore, rigorous performance testing against stringent industry standards assures that only the most robust and resilient spring products arrive on the market. Innovations in this field are rapidly evolving, offering an escalade in protection and efficiency. Consequently, quality investments in these processes do not merely signify added cost but a strategic enhancement of product value, durability, and customer satisfaction.
The resistance to extreme conditions afforded by these treatments enables springs to perform in a variety of challenging environments without faltering. Cleansing protocols, such as pretreatment and surface preparation, serve as the foundational bedrock that both preserves and prepares the substrate for optimal coating adhesion. Budget allocations for high-grade coatings consequently pay dividends in prolonging spring integrity and sustaining performance over extended periods.
Manufacturers stand to gain immeasurably from embedding these sophisticated coatings and treatments into their production ethos. Perspectives shifting towards the longer horizon recognize that such refinements in spring production are not merely enhancements but necessities for staying competitive and surpassing expectations in the dynamic landscape of spring usage and application.
Explore Your Spring Coating Solutions Today
Upgrading your spring components with the right coatings and surface treatments stands at the forefront of ensuring longevity and performance. Recognizing the unique requirements of your application could bring substantial benefits. Engage with surface treatment specialists or coating providers to explore personalized solutions. They will offer insights tailored to your specific needs, guiding you through the selection of materials, application processes, and maintenance strategies.
Have questions about spring coatings or wish to delve deeper into the specifics? Your contributions are valuable. Share your thoughts, inquiries, or feedback in the comments section. This is an invitation to foster an informed community, where knowledge and experiences are exchanged to drive innovation and superior outcomes in the realm of spring coatings and surface treatments.