Conical springs are essential components in various mechanical applications. They provide a unique design that allows for a gradual increase in resistance as they compress. This characteristic makes them suitable for use in automotive suspensions, machinery, battery spring applications, and even household appliances, as offered by an Industrial Spring Company and spring coilers.
Their ability to store and release energy efficiently, despite space constraints, is critical in many systems. Conical springs help absorb shocks and vibrations, contributing to overall stability and performance. Understanding what conical springs are used for can enhance knowledge of their role in engineering and design. This post will explore the diverse applications and benefits of conical springs across different industries.
Key Takeaways
- Conical springs are versatile components used in various industries, including automotive, machinery, aerospace, and construction.
- They provide unique benefits such as space-saving designs and efficient load distribution, making them ideal for compact applications.
- Understanding the different types of conical springs can help you choose the right one for your specific needs based on load and space requirements.
- In automotive applications, conical springs enhance performance by improving suspension systems and reducing vibrations.
- For machinery and equipment, these springs play a crucial role in maintaining stability and supporting heavy loads effectively.
- In construction equipment, conical springs contribute to safety and reliability by ensuring proper function under extreme conditions.
Understanding Conical Springs
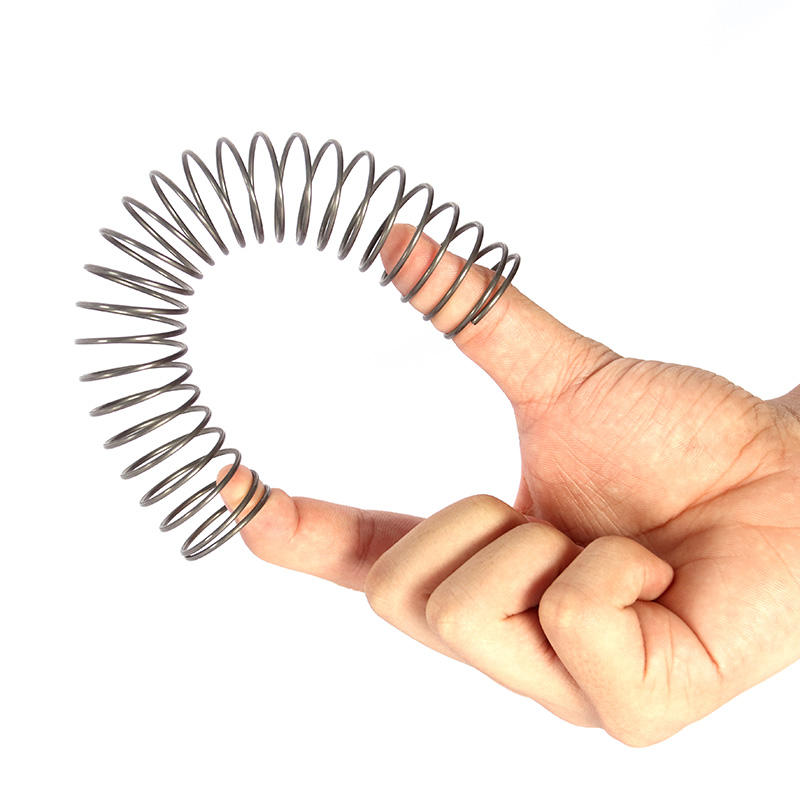
Definition
Conical springs are a type of single coil compression spring shaped like a cone. Their design allows for a gradual taper from a wider base to a narrower top. This unique shape provides several advantages over standard compression springs.
Differences from Other Springs
Conical springs differ significantly from ordinary compression springs. While typical compression springs have uniform diameters throughout their length, conical springs vary in diameter. This variation enables them to handle larger loads while maintaining stability. They also compress more evenly than straight compression springs.
Design Significance
The design of conical springs plays a critical role in preventing buckling and max load deflection. Buckling occurs when a spring is subjected to excessive axial load, leading to structural failure. The tapered shape of conical springs distributes stress more evenly along the coil. This distribution minimizes the risk of buckling under pressure.
Sizing Conical Springs
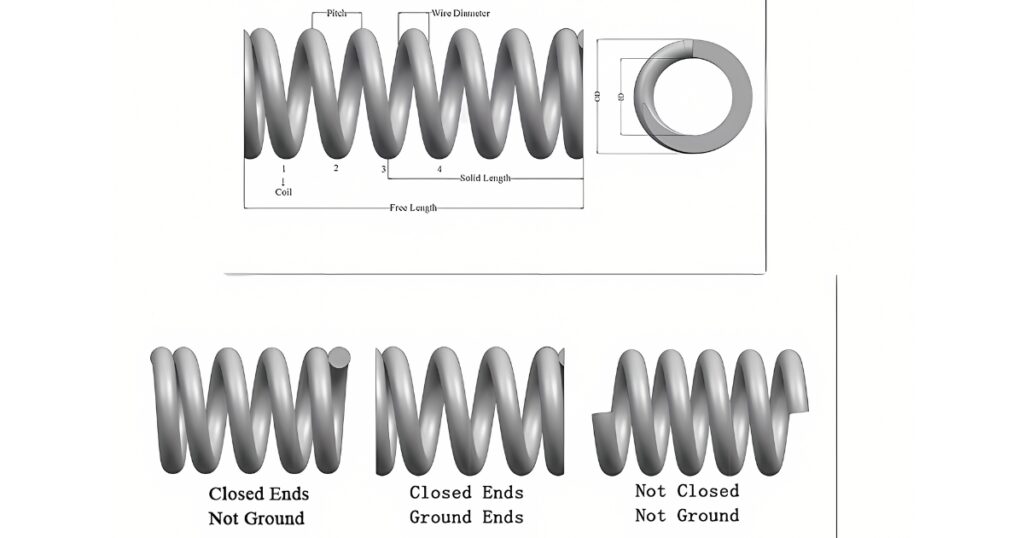
Sizing conical springs involves specific calculations. The conical spring deflection equation helps determine how much a spring will compress under a given load. Proper sizing ensures that the tapered springs, variable diameter springs, and standard springs perform effectively within their intended application under the applied load.
The key factors involved in the calculation include:
- Spring Rate (k): This value can vary along the length of the spring due to the changing coil diameter. It’s typically calculated based on geometry, material, and coil configuration.
- Load (F): The force applied to the spring in Newtons (or pounds).
- Deflection (δ): The amount the spring compresses under a given load.
The deflection of a conical spring under an applied load is determined using a modified version of Hooke’s Law:
F=k⋅δ
To calculate the spring rate for a conical spring:
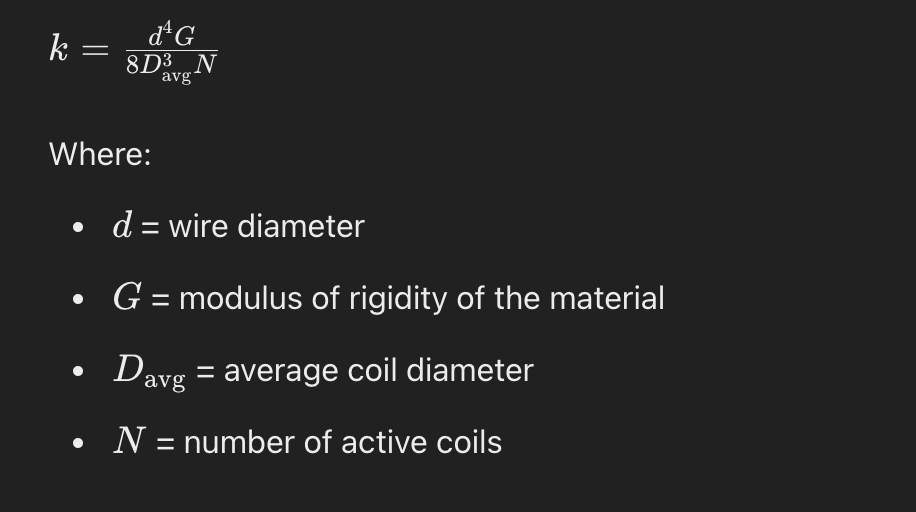
Spring Design Calculations
Typical compression spring design calculations include factors such as wire diameter and coil count. For conical springs, these calculations must account for the cone shape, geometric properties, max load deflection, and maximum deflection per 1.4310 / EN 10270-3:01 Tolerances. Using the conical spring stress equation, engineers can evaluate the maximum load capacity of the spring.
Applications
Conical springs find use in various applications. These include automotive suspensions, aerospace components, and machinery settings. Their ability to absorb shock and provide controlled resistance makes them valuable in these fields.
Unique Features
Several features make conical springs distinct. Their tapered design, similar to conical spring designs, allows for reduced weight without sacrificing strength in conical spring manufacturing. This feature is particularly beneficial in industries where weight savings are crucial, such as aerospace.
Ordering Springs
Ordering conical springs requires precise specifications. Customers need to provide details about dimensions, load requirements, exact spring specifications, Unit of Measure, material type, and characteristics in terms. Manufacturers often offer customization options to meet specific needs.
Benefits of Conical Springs
Space Efficiency
Conical springs offer significant space-saving advantages. Their tapered design allows them to occupy less vertical space compared to regular compression springs. This feature is crucial in applications where height is limited. For instance, in automotive suspension systems, conical springs fit into tighter spaces in metric units while still providing the necessary support.
Their unique shape allows for a compact arrangement. This means that, in simplest terms, manufacturers can design products that are smaller and lighter. The efficient use of space can lead to overall reductions in product size and weight.
Load Handling
Conical designs excel at handling varying loads effectively. These springs can adapt to changes in force due to their geometric shape. When compressed, the conical compression springs’ coils closer to the larger end compress more than those at the smaller end. This characteristic allows them to distribute loads evenly.
In practical terms, this means they perform well in dynamic environments, showcasing optimal functionality and adaptable functionality as observed by the design team regarding their behavior under load. For example, in machinery that experiences fluctuating weights, conical springs provide consistent performance. They help maintain stability and balance under different conditions.
Performance Enhancement
Conical compression springs enhance performance in applications with height restrictions and maximum load in a compact space under compressive load. Their ability to compress into a smaller area makes them ideal for compact devices like portable electronics or medical equipment.
Quality compression springs made from optimum spring materials ensure durability and reliability. This is particularly important in high-stress applications where failure is not an option, especially regarding behavior under load and commitment to quality, as the max load can lead to prolonged delivery time. The design also allows for greater flexibility in engineering solutions.
For example, in robotics, conical springs are used in joints that require precise movement within confined spaces measured in metric units. Their design supports smooth operation without sacrificing strength.
Customization Options
Manufacturers often create custom springs tailored to specific needs. Custom springs can be designed with unique dimensions and material properties, including product details, to optimize performance further. This adaptability adds to the advantages of using conical springs.
By utilizing advanced manufacturing techniques, engineering teams can produce conical springs that meet exact specifications. These custom solutions help industries achieve better results while maintaining efficiency.
Advantages Over Regular Springs
Conical springs have clear advantages over regular compression springs. Regular compression springs exhibit limitations in load distribution, space efficiency, and compressed height. In contrast, conical designs provide superior performance in various applications.
The benefits of using conical springs include:
- Improved load handling.
- Space-saving designs.
- Enhanced performance in restricted areas.
- Customization for specific needs.
These factors make them a preferred choice across a wide selection of multiple industries and a wide range of applications.
Types of Conical Springs
Material Options
Conical springs can be made from various materials. Common choices include steel, stainless steel, and plastic.
Steel is often used for its strength and durability. Manufacturers frequently opt for high-carbon steel due to its excellent elasticity. Stainless steel and alloy steels offer resistance to corrosion, making it ideal for harsh environments.
Plastic conical springs are lightweight and resistant to chemicals. They are suitable for applications where metal springs, such as stainless steel or steel alloys, might corrode, including electrical contacts and battery contacts. Each material has unique properties that affect performance.
Dimensions and Configurations
Conical springs come in different sizes and shapes. They can vary in diameter, length, and coil thickness.
Manufacturers classify these springs based on their dimensions. Standard compression springs have uniform coils, while conical springs taper at one or both ends. This design helps distribute load evenly.
Coil configurations also differ. Some conical springs have a constant pitch between coils, while others may have variable rate varying pitches. These variations affect how the spring compresses under load.
Winding Types
Two primary winding types exist: left-hand and right-hand wound conical springs, with variations in single coil design, active coils, coil diameter, and wire diameter. The direction of the coil determines their classification.
Right-hand wound springs with a wire diameter twist clockwise when viewed from one end. Left-hand wound springs twist counterclockwise. This difference impacts how they behave under tension or compression.
Applications often dictate which winding type to use. Right-hand wound music wire springs are more common in many devices. Left-hand wound options may be necessary for specific mechanical systems.
How Conical Springs Work
Compression Mechanics
Conical springs operate through compression and tension. When a force is applied, the spring compresses. This compression stores energy within the coil. The tighter the spring compresses, the more energy it stores. Once the force is removed, the spring expands back to its original shape at its natural period. This process releases the stored energy.
The design of conical springs allows them to handle varying loads effectively. As one end of the conical compression springs compresses, the other end can still maintain its shape. This unique feature enables them to absorb shocks in various applications.
Tapering Design
The tapered shape and tapering design of conical springs influences load distribution significantly. The top of the spring is wider than the bottom. This shape allows for more efficient handling of forces. The wider base provides stability while supporting heavier loads.
Load distribution is essential in applications like automotive suspensions. Here, conical springs help balance weight across different components. They prevent uneven wear and tear. Proper load distribution ensures that vehicles handle well on various terrains and vibration loads.
Energy Storage
Energy storage and release are crucial functions of conical springs. When compressed, these springs store potential energy. This energy, due to the initial tension, is released when the spring returns to its original position during its natural period.
This process is evident in many devices, such as cameras and toys, in simplest terms related to art manufacturing equipment and control systems. In cameras, conical springs help with shutter mechanisms. They ensure quick and precise movement when taking photos. In toys, they provide action and reaction during play.
Conical springs also find use in machinery such as stamping presses and art manufacturing equipment where controlled movement is necessary. They help maintain tension in belts and chains, ensuring smooth operation.
Applications in Automotive Industry
Suspension Systems
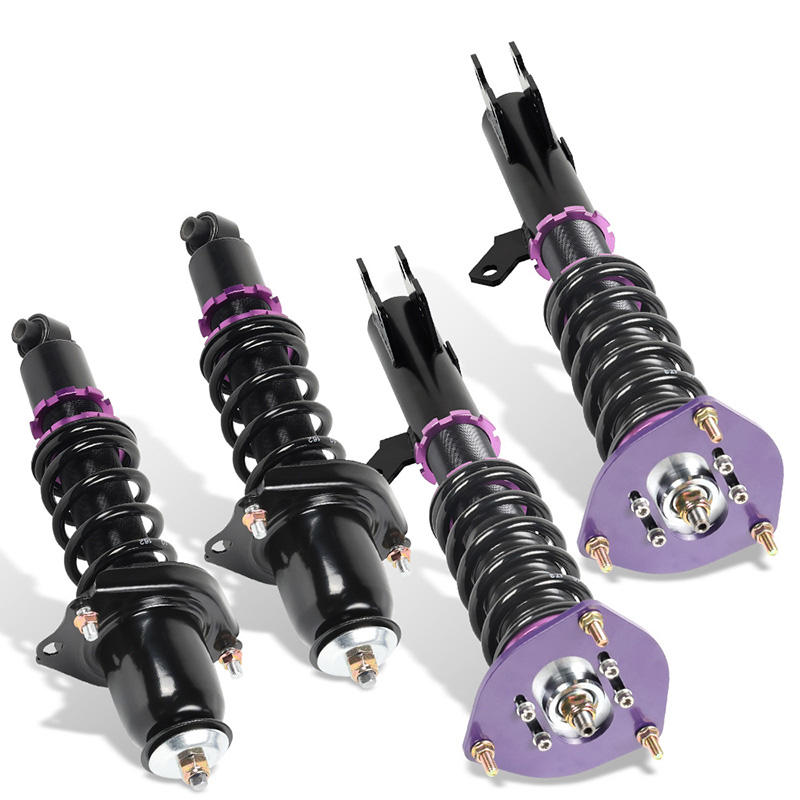
Conical springs play a vital role in vehicle suspension systems. They help maintain the vehicle’s height and improve stability. These springs allow for deflection under vibration loads, which absorbs shocks from the road. This action keeps the tires in contact with the surface, enhancing traction.
Designers use conical springs to optimize space within the suspension system. Their conical design and asymmetrical shapes allow them to fit into compact spaces while providing a combination of flexibility and necessary support. When a vehicle hits a bump, these springs compress and expand. This process reduces the impact felt by passengers.
Shock Absorbers
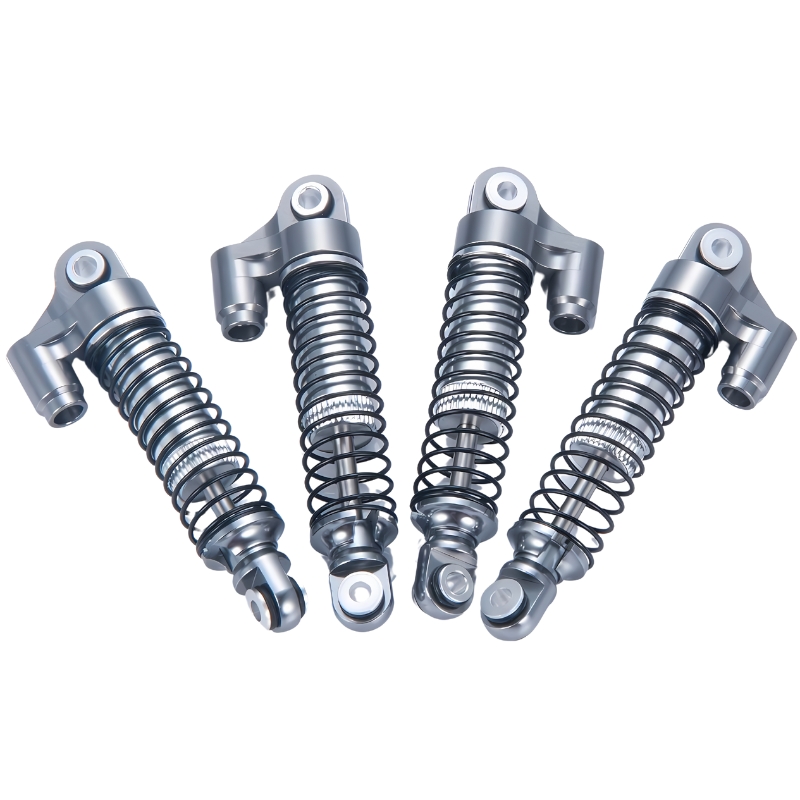
Conical springs are also essential components of shock absorbers. They work alongside hydraulic fluid to dampen vibrations. The spring’s unique design allows it to handle varied loads effectively. As the vehicle moves over uneven terrain, the advantage of banana springs allows the spring to compress, helping to manage energy transfer.
In shock absorber assemblies, conical springs provide consistent performance. They help control the rebound of the shock absorber after compression, including factors like spring rate and contact spring. This function is crucial for maintaining ride comfort and safety.
Strut Assemblies
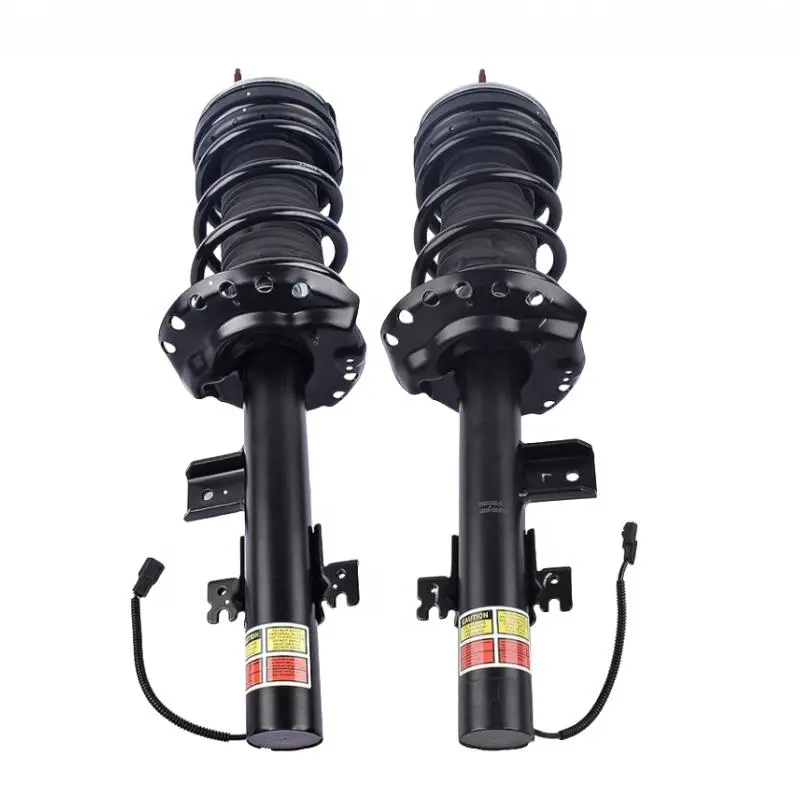
In strut assemblies, conical springs contribute significantly to overall vehicle dynamics in automotive suspension systems. These springs support both the weight of the vehicle and the forces during cornering. When turning, they help maintain proper alignment of the wheels.
Struts equipped with conical springs improve handling characteristics. They allow for better steering response and stability during maneuvers. Drivers experience enhanced control thanks to these components.
Ride Comfort and Handling
The use of conical springs improves both ride comfort and handling in vehicles. By absorbing shocks and vibrations, they create a smoother driving experience. Passengers feel less jarring when traveling over rough surfaces.
Moreover, their ability to maintain tire contact enhances handling. This feature allows drivers to navigate turns with confidence. The blend of quality parts in the balance provided by conical springs contributes to overall vehicle performance.
Summary of Applications
Conical springs serve multiple purposes in the automotive industry:
- Suspension systems: Maintain vehicle height and stability.
- Shock absorbers: Dampen vibrations and manage energy transfer.
- Strut assemblies: Support weight and enhance handling.
These applications showcase how crucial conical springs are for automotive suspension systems in modern vehicles, particularly those using chrome silicon. Their design optimizes space while improving comfort and control.
Uses in Machinery and Equipment
Industrial Machinery
Conical springs find extensive use in industrial machinery. They support various mechanical components. These springs absorb shock and provide stability in machines. Their design allows for effective compression without buckling. This is crucial in heavy-duty applications.
In many industrial settings, conical springs control the movement of parts. For instance, they are often used in presses, conveyor systems, and conical spring applications. The unique shape helps manage force distribution effectively. As a result, they enhance the overall reliability of machinery.
Force Control
Controlling force is essential in mechanical systems. Conical springs play a vital role in this process. They can adjust to varying loads while maintaining their shape, providing additional flexibility and a combination of flexibility, additional stability, and constant spring rate varieties. This ability prevents deformation over time.
These springs also help maintain uniform contact between moving parts, electrical contacts, and battery contacts. This reduces wear and tear on equipment. In applications like clutches and brakes, they ensure smooth operation. A consistent rate of compression contributes to better performance.
Efficiency Enhancement
Efficiency is key in any mechanical system. Conical springs contribute significantly to enhancing efficiency. Their specific design allows for optimal functionality and load capacities, optimizing space usage within equipment. They can fit into tighter spaces compared to traditional coil springs.
Moreover, they reduce energy loss during operation. By controlling movement effectively, these springs minimize unnecessary friction. This leads to smoother operations and longer lifespan for industrial equipment and a blend of quality parts in machinery components.
Types of Conical Springs
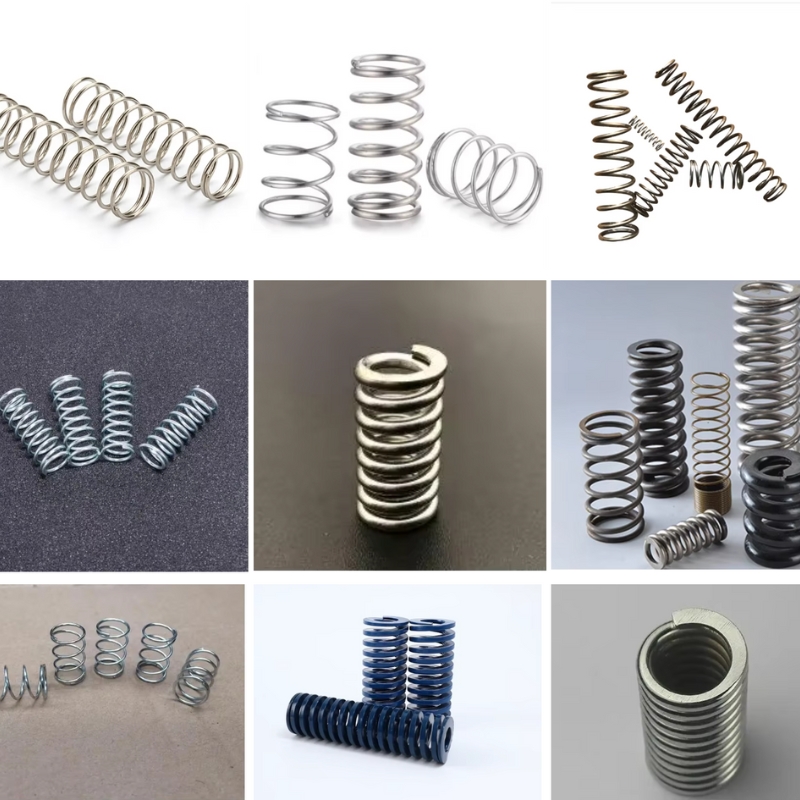
Different types of conical springs exist based on their application, such as Carbon Steel or Stainless Steel. Some are designed for high-load capacity, while others focus on precision movements. Understanding the type required is crucial for optimal performance.
- Compression Springs: Used primarily in applications requiring force absorption.
- Extension Springs: Useful where pulling forces are needed.
- Torsion Springs: Designed for twisting motions in various devices.
Each type serves a specific purpose within major appliances, machinery, and equipment.
Role in Aerospace Sector
Aircraft Safety
Conical springs play a crucial role in enhancing aircraft safety mechanisms. They absorb shocks and vibrations during flight. This function is vital for maintaining the integrity of essential components in various systems, including Stanley Spring. For instance, they help stabilize control surfaces like ailerons and elevators. These components are essential for maneuverability and overall flight stability.
In emergencies, conical springs ensure that safety systems activate correctly. They can be found in emergency deployment mechanisms. This includes systems like parachutes or emergency slides. Their reliable performance, backed by a team of experts and a commitment to quality, can make a significant difference during critical moments, providing enhanced stability and additional stability.
Landing Gear
Conical springs are integral to aircraft landing gear systems. They provide effective shock absorption when an aircraft lands. The force of landing, under the applied load, can be immense, and these springs help mitigate that impact. They allow the landing gear to compress and expand smoothly.
This compression reduces stress on the airframe. It prevents damage to sensitive components within the aircraft. The design of conical springs allows them to fit into tight spaces efficiently. This feature is essential in the compact designs of modern aircraft in aerospace industries.
Control Surfaces
Control surfaces also benefit from the use of conical springs. These springs assist in maintaining tension on control cables. They ensure that pilots have responsive control over the aircraft’s movements. This responsiveness is vital for safe navigation through various flight conditions, ensuring lateral stability and achieving fourteen to two-hundred-and-eighty results.
The precision of control surfaces directly affects the aircraft’s performance. Conical springs contribute to this precision by providing constant coils, uniform pitch, and consistent tension with advanced coiling equipment and constant pitch. Pilots rely on this reliability during critical phases of flight, such as takeoff and landing.
Weight Reduction
Weight reduction is another significant advantage of using conical springs in aerospace applications. Aircraft manufacturers in the aerospace industries strive to create lighter planes without sacrificing strength or safety. Conical springs offer a solution to this challenge.
These springs are designed to be lightweight while still providing high strength, whether made of Carbon Steel or Stainless Steel. Their unique shape allows for efficient load distribution. This means they can handle heavy loads without adding unnecessary weight.
Using conical springs helps engineers meet strict weight requirements set by aviation regulations. Lighter aircraft consume less fuel and have better performance metrics. This efficiency leads to lower operational costs over time.
Importance in Construction Equipment
Heavy Machinery
Conical springs play a vital role in heavy machinery. They are commonly used in construction equipment like excavators, bulldozers, and cranes. These springs provide essential support and flexibility. Their quality design allows them to handle heavy loads while maintaining stability.
The unique shape of conical springs helps distribute weight evenly. This feature is crucial for machinery with variable pitch that operates on uneven terrain. The diameter and height of the springs can be adjusted based on the specific needs of the equipment. This customization enhances performance and safety during operation.
Vibration Dampening
Vibration dampening is another critical function of conical springs. Construction sites often expose equipment to harsh conditions. Vibrations can lead to wear and tear over time. Conical springs absorb these vibrations effectively. They reduce stress on other major appliances, extending the lifespan of the machinery.
By minimizing vibrations, these springs improve operator comfort as well. A smoother ride leads to better control and precision when using heavy tools. Operators can work more efficiently with less fatigue.
Load Stabilization
Load stabilization is essential in construction operations. Conical springs help maintain balance when lifting heavy materials. They adjust to changes in weight distribution and constant spring rates, ensuring stability throughout the process.
For instance, when an excavator lifts a large load, the conical spring compensates for shifts in weight. This adjustment prevents tipping and enhances safety on site. The reliability of construction equipment directly impacts project timelines and costs.
Durability and Reliability
Durability is a key factor in construction equipment performance. Conical springs are designed to withstand extreme conditions. They resist corrosion and fatigue on the outer surface, making them suitable for outdoor use with surface treatment.
Reliability is equally important for construction projects. Equipment downtime can lead to significant delays. Conical springs contribute to the overall reliability of machines by reducing maintenance needs. Their robust construction ensures they perform consistently under pressure.
Construction companies prioritize equipment from Industrial Spring Company that offers both quality and longevity. Conical springs meet these requirements effectively. Their ability to enhance performance makes them indispensable in the industry.
Closing Thoughts
Conical springs play a crucial role across various industries, including automotive, aerospace, machinery, and construction. Their unique design allows for effective load distribution and space efficiency, making them indispensable components in numerous applications. Understanding their functionality and benefits highlights their significance as essential components in enhancing performance and safety.
The diverse applications of conical springs underscore their importance in modern engineering. As industries continue to evolve, the demand for innovative spring solutions will likely increase. Stakeholders should consider the potential of conical springs under concentrated load in optimizing their designs and operations. Further exploration of this topic can lead to improved practices and advancements in technology.
Frequently Asked Questions
What are conical springs?
Conical springs are helical springs that taper from a larger diameter to a smaller one. They provide variable resistance and are designed to compress or expand under load, making them effective in various stock compression spring applications and standard compression spring designs.
How do conical springs differ from regular springs?
Conical springs differ by their shape and load distribution. Their tapered design, with a conical shape, allows for a more compact form factor and provides progressive resistance with rate linearity tolerance, unlike regular cylindrical springs that maintain uniform resistance throughout compression.
What materials are commonly used for conical springs?
Common materials for conical springs include stainless steel, carbon steel, and various alloys. These stainless steel materials offer durability, corrosion resistance, and the ability to withstand high stress, along with steel alloys and surface treatment.
Where are conical springs typically used?
Conical springs are widely used in automotive applications, machinery, aerospace, and construction equipment. Their versatility, along with a wide selection from the Spring Finder, makes them suitable for various mechanical systems requiring reliable force application.
What advantages do conical springs offer?
Conical springs provide several advantages, including space savings due to their tapered design, adjustable stiffness, and improved energy absorption. These features enhance performance in dynamic applications.
Can conical springs be customized?
Yes, conical springs can be customized in terms of dimensions, material, and coil configuration. Customization allows them to meet specific load requirements, fit unique application needs, and consider material choice, conical spring design options, product details, and spring specification.
Are there any limitations to using conical springs?
While conical springs offer many benefits, they may have limitations in terms of maximum load capacity and fatigue life compared to other spring types. Proper engineering design is essential to ensure optimal performance.