Dive into the essential world of clock spring with our guide, “What is a Clock Spring?” Perfect for enthusiasts and professionals alike, this exploration reveals how these critical components power modern devices and machinery. Elevate your knowledge and innovate your projects. Start your journey now!
What is a Clock Spring?
A clock spring is a mechanical component designed as a coiled strip of metal that stores and releases rotational energy. Originally used in timepieces to power the movement of hands for accurate timekeeping, its applications have expanded to automotive, electronics, and various industrial uses. Clock springs can unwind to release energy in a controlled manner, making them essential for mechanisms that require consistent, prolonged force.
Other Names for Clock Spring
Clock springs, essential components in various mechanical and electronic devices, go by several names that reflect their diverse applications and design characteristics. Here’s a detailed look at each alternative name:
- Spiral Springs: Named for their coiled, spiral shape, these springs efficiently store and release mechanical energy. The spiral design is crucial for compactness and the consistent release of energy, making them ideal for devices requiring a smooth operation over time.
- Power Springs: This term emphasizes the spring’s role in storing significant amounts of energy that can be released to power a mechanism. Power springs are fundamental in applications where a controlled and sustained release of energy is necessary for the operation, such as in mechanical watches or retractable devices.
- Mainsprings: Specifically used within the context of timekeeping devices like watches and clocks, mainsprings denote the primary spring responsible for driving the mechanism. Their ability to store and methodically release energy makes accurate timekeeping possible, showcasing the precision engineering of these components.
- Motor Springs: Highlighting their application in providing motive force, motor springs are used in various mechanical devices to impart movement or energy. These springs are integral to the functioning of motors and other mechanical assemblies where a reliable source of energy is critical for operation.
- Coil Springs: A broad term that refers to the spring’s coiled configuration. Coil springs can be designed to meet a wide range of mechanical needs, from absorbing shock to maintaining force or tension within a mechanism. Their versatility makes them suitable for countless applications across different industries.
- Torsion Springs: This name is given to springs that operate on the principle of torsion or twisting. They exert a torque or rotational force when twisted, ideal for applications requiring rotational motion such as levers, doors, and other mechanisms that pivot or turn.
- Flat Springs: These are described by their flat, thin strip of metal wound into a coil, focusing on the spring’s slim profile and the specific applications where space efficiency and compact design are necessary. Flat springs offer a unique solution for space-constrained environments while still providing the necessary force or tension.
Each of these names – from Spiral Springs to Flat Springs – captures a unique aspect of the clock spring’s functionality, design, or application area. Their versatility and ability to store and release energy in a controlled manner make them indispensable components in the design of mechanical and electronic systems, illustrating the ingenious application of basic physical principles to solve complex engineering challenges.
What are the symptoms of a bad clock spring
The symptoms of a bad clock spring include various indicators that can help identify issues with this component in a vehicle’s steering system. Some common signs of a faulty clock spring are:
- Inoperative Horn: When the clock spring fails, the horn may not work at all or only work intermittently, which is a critical safety concern as it affects the vehicle’s signaling capabilities.
- Airbag Warning Light: A malfunctioning clock spring can trigger the airbag warning light on the dashboard, indicating a potential problem with the airbag system’s functionality.
- Inoperable Steering Wheel Buttons: Failure of the clock spring can lead to the loss of functionality in steering wheel buttons, such as those for cruise control, radio controls, and other accessories mounted on the steering wheel.
- Intermittent Loss of Electrical Functions: The symptoms of a bad clock spring can manifest intermittently, where certain functions like the horn, radio buttons, or cruise control may work sporadically depending on the position of the steering wheel.
Identifying these symptoms is crucial as a faulty clock spring can impact critical safety features like the airbag system and the overall functionality of the steering wheel controls. If any of these signs are noticed, it is recommended to have the clock spring inspected and replaced promptly to ensure the safe operation of the vehicle.
What causes a clock spring to fail
Clock spring failure is influenced by a combination of physical wear, environmental conditions, mechanical stress, and maintenance practices. Some common causes of clock spring failure include:
- Brittle Wires: Over time, the wires within the clock spring can become brittle and break, especially in certain units where the wires are prone to wear and tear.
- Improper Installation or Damage: Clock springs can fail if they are improperly installed or damaged during maintenance or repair work. For instance, if the steering wheel is not held stationary while other components are being replaced, it can result in damage to the clock spring.
- Debris Contamination: Debris, such as strands of hair or other contaminants, can enter the clock spring and disrupt its inner workings. This contamination can displace guide loops inside the spring, leading to excess tension and potential damage to the ribbon cable within the clock spring.
- Overzealous Technicians: Clock springs can also fail due to mishandling by technicians who may damage the component or reinstall it improperly after maintenance work, causing issues with the electrical connections between the steering wheel and the vehicle’s computers.
- Normal Wear and Tear: Like any mechanical component, clock springs can deteriorate over time due to regular use and age, leading to a loss of flexibility and functionality.
- Moisture and Corrosion: Exposure to moisture, either from vehicle interior leaks or high humidity, can lead to corrosion of the clock spring’s metal components, impairing its function.
- Electrical Overloads: Surges in the vehicle’s electrical system can burn out or damage the clock spring’s delicate wiring.
Identifying these causes of clock spring failure is essential for timely diagnosis and repair to ensure the proper functioning of critical systems like the airbag and steering wheel controls in a vehicle.
How long does a clock spring typically last
Clock springs are engineered to be durable, with many designed to last for the entire lifespan of the vehicle. Typically, a clock spring’s longevity ranges from 80,000 to 150,000 miles, although high-quality components in well-maintained vehicles under normal driving conditions might never require replacement. However, their durability can be compromised by factors such as wear and tear, improper handling during maintenance, contamination by debris, or damage inflicted by overzealous technicians. Over time, certain clock springs may experience issues where the wires become brittle and break, necessitating a replacement.
While clock springs are intended to be long-lasting, ensuring the continuous operation of critical safety and convenience features such as airbag systems, steering wheel controls, and the horn, it is crucial to remain vigilant for signs of failure. Symptoms like an inoperative horn, airbag warning lights, or malfunctioning steering wheel controls can indicate a failing clock spring. Recognizing and addressing these signs promptly is essential for maintaining the vehicle’s safety and functionality. Therefore, despite their designed durability, monitoring for any indication of clock spring failure and seeking timely repair or replacement is key to ensuring the continued safety and operational integrity of the vehicle’s steering system.
Applications of Clock Springs
Clock springs, also known as power springs, are utilized in various applications that require rotational energy storage and release. Some common applications of clock springs include:
- Clocks and Watches: Clock springs are commonly used in timepieces like clocks and watches, where they provide the necessary torque for the movement of clock hands and watch mechanisms.
- Automotive Industry: In the automotive sector, clock springs play a crucial role in steering wheel mechanisms. They ensure continuous connectivity for electrical systems in vehicles, allowing for the operation of steering wheel controls and airbag deployment regardless of the steering wheel’s movement.
- Healthcare and Medical Devices: Clock springs are employed in medical equipment such as MRI machines and other healthcare devices. They contribute to the functionality of these devices by providing rotational energy storage and release as needed.
- Industrial Applications: Clock springs find applications in various industrial settings where rotational torque is required. They are used in machinery, equipment, and systems that necessitate circular movement and torque generation.
- Toys and Games: Clock springs are utilized in toys like music boxes and wind-up toys, providing the necessary energy for these devices to function. They enable the winding up and gradual release of energy to power the movement of toys and games.
- Timing Devices: Clock springs are essential components in timing devices, ensuring the accurate operation of mechanisms that rely on precise timing. They contribute to the functionality of devices like timers and meters.
- Architectural Hardware: Clock springs are also used in architectural hardware applications where rotational energy storage and release are required. They can be found in various hardware components that involve circular movement and torque generation.
Clock springs are versatile components that offer a cost-effective solution for applications requiring rotational energy storage and release. Their widespread use across different industries highlights their importance in various mechanical systems and devices.
Design Consideration for Custom Clock Springs
Designing custom clock springs involves a meticulous blend of engineering precision, material science, and understanding of the application’s specific requirements. The process is critical to ensure that the clock spring not only fits within its designated space but also performs its required function flawlessly over its intended lifespan. Here are key considerations in the design of custom clock springs:
1. Application Requirements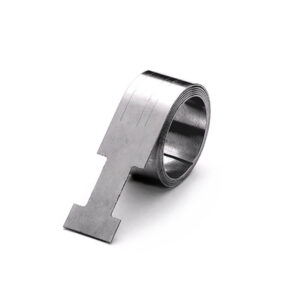
Understanding the application’s needs is foundational. This includes the operational environment (temperature, humidity, exposure to chemicals), the expected lifespan, and the mechanical requirements (force, torque, rotational degrees).
2. Material Selection
The choice of material impacts the spring’s durability, flexibility, and resistance to environmental conditions. Common materials include high-carbon steel, stainless steel, and nickel alloys, each offering different properties in terms of strength, corrosion resistance, and cost-effectiveness.
3. Spring Geometry
The dimensions of the clock spring, including its thickness, width, and total coil length, are designed to meet the specific torque and space requirements of the application. This also involves deciding on the spring’s end configuration for attachment to the mechanism it will drive or be part of.
4. Tension and Torque Requirements
The amount of energy the spring needs to store and release dictates its design. Engineers calculate the required preload tension, the maximum extended length, and the torque to ensure the spring can deliver the necessary mechanical energy without failing.
5. Stress and Fatigue Analysis
Custom clock springs must withstand repeated cycles of winding and unwinding without significant degradation. Stress analysis helps in predicting potential failure points, while fatigue analysis ensures the spring can endure the expected number of cycles throughout its service life.
6. Environmental Considerations
Factors like temperature extremes, moisture, and exposure to corrosive substances affect the spring’s material and coating choices. For instance, springs used in outdoor applications may require additional corrosion resistance.
Unlock the full potential of your mechanisms with Zigoal’s custom clock springs. Tailored to meet your precise specifications, our clock spring design promise unmatched quality, durability, and performance. Contact Zigoal today to elevate your projects with our clock spring experts.