The realm of mechanical engineering has witnessed a remarkable evolution in spring technology. Innovations have led to an astounding 70 trillion unique configurations of coil compression springs, revolutionizing industries from automotive to aerospace.
This unprecedented level of customization allows engineers to fine-tune designs for specific applications with unparalleled precision.
Advanced alloys and innovative production methods have opened up new horizons, enabling the creation of springs that are lighter, stronger, and more durable than ever before.
The coil spring landscape now offers an impressive array of options, requiring careful consideration of materials, manufacturing techniques, and precise specifications to achieve optimal performance. Product versatility has been significantly enhanced, empowering engineers to meet diverse requirements across various sectors. The vast number of coil spring design possibilities, considering factors like compression, torsion, dimension, force, and engineering tolerances, leads to an estimated 70 trillion potential stock spring configurations.
Understanding Helical Mechanics
Understanding helical components is vital for their optimal use in industries, especially for coil compression applications. These coiled structures are fundamental in industrial engineering for energy storage and force distribution. Distributors and suppliers must comprehend the mechanics of helical structures to select appropriate components effectively.
Key Principles:
- Helical Structure: Follows a spiral path around a central axis, affecting deflection.
- Design Parameters: Pitch, diameter, and wire gauge influence performance. Tighter coils are stiffer, while wider coils are more flexible.
- Types: Compression springs resist compressive forces, extension springs store energy when stretched, and torsion springs handle rotational forces.
Design Considerations:
- Application Requirements: Analyze specific needs for compression, extension, or torsion.
- Stress Factors: Consider intended function and environmental impacts to determine the appropriate spring type.
- Selection Criteria: Deflection, torsion, length, stress, and tensile strength must be evaluated.
- Material Selection: Choose alloys based on corrosion resistance, durability, and temperature tolerance.
For Distributors:
- Tailored Solutions: Assess working loads, dimensions, and industry-specific needs.
- Tools: Utilize modern design tools and spring calculators to determine optimal configurations, including spring rate, free length, and wire diameter.
- Key Factors: Required force, available space, operating environment, and component lifespan.
- Material Properties: Ensure tensile strength and corrosion resistance match application demands.
Applications: Helical components are essential in various industrial settings, providing reliability and performance. Mastery of helical mechanics enables professionals to innovate and meet complex application requirements effectively.
By focusing on these core elements, distributors can offer the best helical spring solutions, ensuring optimal performance and longevity for their clients across multiple industries.
Optimizing Compression Performance
Key Factors:
- Efficiency & Durability: Essential in helical mechanics.
- Material Choice:
- Alloys: Inconel, Elgiloy for resilience and longevity.
- Production Methods:
- High-Tech: Enhances coil consistency and surface quality.
- Innovative Designs:
- Variable Pitch & Conical Shapes: Increase load capacity.
Enhancements:
- Specialized Treatments: Reduce wear and extend operational life.
- Stress Relief: Ensures long-term stability under repeated loading.
Evaluation Metrics:
- Material Composition
- Load Ratings
- Fatigue Resistance
- Testing Data: Detailed specifications from top manufacturers.
- Cost vs. Performance: Balance to choose optimal components.
Comparative Insights:
- Premium Alloys vs. Stainless Steel:
- Inconel, Elgiloy: Superior durability in harsh environments.
- Special Coatings:
- Corrosion Resistance: Up to 500% improvement.
Maintenance Practices:
- Regular Inspections: Check for wear, corrosion, deformation.
- Lubrication Schedule: Reduces friction, extends lifespan.
- Protective Measures:
- Barriers or Sacrificial Anodes: Prevent material degradation in corrosive environments.
Advanced Testing Methods:
- Finite Element Analysis (FEA): Predicts performance under various conditions.
- Accelerated Life Testing: Optimizes spring performance for specific applications.
Benefits:
- Data-Driven Optimization: Tailored springs for specific industrial needs.
- Maximized Efficiency & Reliability: Ensures peak performance and longevity.
By focusing on these elements, manufacturers can enhance compression device performance, ensuring high efficiency and durability for industrial applications.
Spring Efficiency Enhancements
- Advanced alloys offer exceptional resilience and durability
- Novel spring designs like variable pitch can boost load capacity
- Specialized surface treatments reduce wear and extend operational life
- Regular maintenance and proper lubrication significantly increase lifespan
- Finite element analysis aids in optimizing spring performance for specific applications
Product Comparisons
Material |
Corrosion Resistance |
Load Capacity |
Lifespan |
Standard Stainless Steel |
Good |
Moderate |
Average |
Inconel |
Excellent |
High |
Extended |
Elgiloy |
Superior |
Very High |
Longest |
Maintenance Tips for Industrial Springs
- Conduct regular visual inspections for signs of wear or damage
- Implement a consistent lubrication schedule
- Clean springs regularly to remove debris and contaminants
- Monitor operating conditions and adjust maintenance frequency as needed
- Replace springs before they reach critical fatigue levels
Torsion And Tension Explained
- Torsion:
- Involves twisting forces.
- Requires materials with higher wire diameters for twisting stress resistance.
- Tension:
- Involves stretching forces.
- Focuses on elongation properties.
Material Selection & Geometry:
- Torsion Springs:
- Use thicker wires to endure twisting.
- Tension Springs:
- Emphasize materials that allow for significant elongation.
Industry Applications:
- Automotive:
- Torsion Bars: Support suspension systems for stability and comfort.
- Tension Springs: Utilize in throttle mechanisms for precise control.
- Aerospace:
- Balance torsional and tensile forces.
- Critical spring rate calculations for reliability under extreme conditions.
- Medical Devices:
- Torsion Springs: Provide precise control in surgical instruments.
- Tension Springs: Used in rehabilitation equipment.
- Electronics:
- Tension Springs: Found in switches and connectors.
- Torsion Springs: Used in hinges for laptops and tablets.
Design Considerations:
- Wire Diameter: Crucial for handling specific forces.
- Spring Rate: Determines how the spring responds to forces.
- Overall Design: Tailored to meet application-specific requirements.
For Distributors and Engineers:
- Understanding Applications:
- Recognize unique needs for torsion vs. tension springs.
- Selection Factors:
- Wire diameter, spring rate, material properties.
- Targeted Solutions:
- Provide springs that ensure optimal performance and reliability across industries.
Technological Advances:
- Complex Force Handling: Developing springs that manage combined torsional and tensile forces.
- Innovation: Keeping up with advancements to offer cutting-edge solutions.
Maintenance and Reliability:
- Regular Inspections: Check for wear, corrosion, and deformation.
- Lubrication: Reduces friction and extends spring lifespan.
- Protective Measures: Use barriers or sacrificial anodes in corrosive environments.
Benefits:
- Optimized Performance: Tailored springs meet specific industrial needs.
- Enhanced Reliability: Ensures long-term functionality in various applications.
- Industry Versatility: Supports a wide range of sectors from heavy machinery to delicate instruments.
By understanding the roles of torsion and tension in spring design, distributors and engineers can create effective, reliable solutions tailored to diverse industrial applications, fostering innovation and efficiency.
Designing For Ultimate Strength
Our focus now turns to maximizing spring strength for the correct spring application. Engineers push wire compression limits through new practices. The search for better performance while keeping elasticity drives new ideas in materials and treatments.
Advanced Materials are essential for developing high-performance coil compression springs for Higher Strength
New alloys, like nickel-titanium and cobalt-chromium, offer better strength-to-weight ratios than usual options. These materials allow for springs that can handle greater forces while staying flexible. Special heat treatments, such as precipitation hardening and cryogenic processing, boost the mechanical properties of these materials, resulting in stock compression springs with unmatched durability and resilience.
Balancing Strength and Flexibility
Ultimate strength ratings vary across products, with factors like wire diameter, shape, and material affecting a spring’s strength-to-flexibility ratio. Engineers must balance these factors to get the best performance for specific uses. This careful approach ensures springs can meet the tough needs of various industries, from aerospace to medical devices.
Computer-Aided Design for Optimal Performance
Creating high-strength springs often uses advanced computer modeling and simulation tools. These technologies help engineers predict and improve spring behavior under various stress conditions, leading to more efficient and reliable designs. By using these tools, manufacturers can create springs that push the limits of what was thought possible in terms of strength and durability, ensuring the correct spring for every application.
Considerations for High-Stress Applications
When choosing springs for high-stress uses, it’s important to think about not just the ultimate strength but also fatigue resistance and environmental factors. Some advanced alloys offer better corrosion resistance, making them ideal for harsh environments where traditional materials would quickly wear down. This mix of strength and durability can greatly extend the life of spring-based parts, reducing maintenance costs and improving overall system reliability.
Advanced Materials |
Conventional Materials |
Exceptional strength-to-weight ratio |
Lower strength-to-weight ratio |
Nickel-titanium and cobalt-chromium alloys |
Steel and other traditional metals |
Enhanced performance through specialized treatments |
Limited performance enhancement options |
Superior fatigue resistance |
Standard fatigue resistance |
High corrosion resistance |
Variable corrosion resistance |
The quest for ultimate strength in spring design keeps driving new ideas in the field. As new materials and manufacturing methods appear, the chances for creating stronger, more durable springs grow. This ongoing change ensures that springs stay at the forefront of engineering solutions, meeting the growing demands of modern technology and industry.
Calculating Dimensional Parameters
Understanding spring dimensions is key for creating reliable components across industries. Precise measurements and formulas form the basis for effective spring design. Wire diameter, mean coil diameter, pitch, free length, and solid height are crucial parameters.
Essential formulas for spring calculations include:
- Wire diameter (d) = √(8FD/πτ), where F is force, D is mean diameter, and τ is shear stress
- Mean diameter (D) = Outside diameter – Wire diameter
- Free length = (Number of active turns x Wire diameter) + (2 x Solid height) for compression spring designs
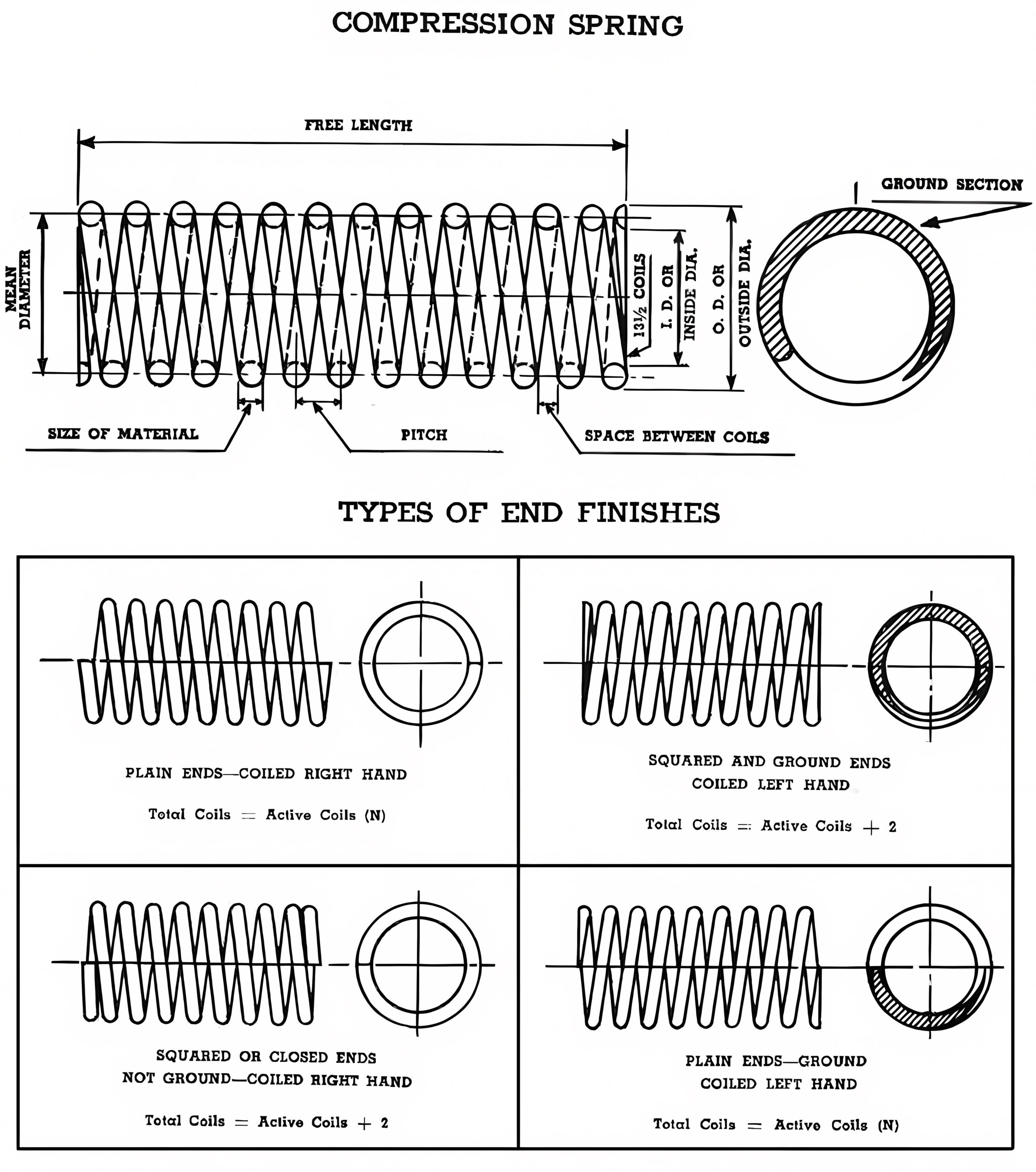
Spring specifications often need tight tolerances to ensure the spring must perform correctly. Temperature changes and material properties can affect dimensions. Modern tools allow for more accurate spring creation and quality control.
Small changes in wire diameter or length significantly impact spring rate and load capacity. Knowing these relationships helps in picking the right spring for specific uses.
New materials and methods have expanded spring design options. Electronics need ultra-fine wire springs, while heavy machinery may need springs with larger wire diameters for extreme loads.
The operating environment is crucial when specifying spring dimensions. Corrosion, temperature extremes, and cyclic loading can all affect the best dimensions for a given use.
Parameter |
Importance |
Considerations |
Wire Diameter |
Sets strength and rate for the coil compression spring to achieve optimal performance. |
Material properties, load needs |
Mean Diameter |
Affects spring index and stability |
Space limits, buckling risk |
Free Length |
Sets initial position and travel |
Installation space, required deflection |
Pitch |
Influences rate and solid height |
Progressive or linear rate needs |
Mastering dimensional parameters allows for tailored solutions that meet exact industry needs. This knowledge ensures optimal spring performance and adds to the overall efficiency of systems using these key parts.
For complex spring designs, using a spring calculator can help determine the correct coil spring specifications. These tools often include options for compression spring, extension spring, and torsion spring types.
When working with
custom springs, consider factors like:
- Required force at specific deflection points
- Available space for the spring
- Operating temperature range
- Expected cycle life
- Material choice based on environment (e.g., corrosion resistance)
Remember, the spring constant (k) is a key factor in spring design. It’s calculated using the formula: k = (Gd^4) / (8D^3N), where G is the shear modulus, d is wire diameter, D is mean coil diameter, and N is the number of active coils.
For stock springs, a spring finder tool can help locate the right product quickly. These tools often allow searching by key parameters like wire diameter, free length, and spring rate.
Exploring Material Choices
After looking at spring strength and size factors, choosing the right material becomes crucial for spring performance. The material affects how long a spring lasts, how it handles harsh conditions, and how well it works under repeated stress. Engineers must carefully weigh several factors when picking materials to ensure springs work well in different industrial settings.
Stainless steel is known for resisting rust, making it great for marine or chemical uses where springs face tough conditions. It fights off rust and chemical damage, ensuring long life in harsh environments, but may cost more than other options.
High-carbon steel offers top strength, ideal for heavy-duty industrial springs that need to handle high stress and are required to move the spring effectively. This material shines in uses requiring significant load-bearing ability but may rust easier than stainless steel.
New alloys are improving spring performance, offering better fatigue life and stress resistance. Nickel-based alloys, for example, resist rust well and offer high strength, suiting them for extreme temperature uses. However, their higher cost often limits them to special industries.
Beryllium copper alloys provide a mix of high strength, good electrical flow, and non-magnetic properties. These traits make them valuable in electronic and aerospace uses, though handling them requires care due to potential health risks.
When choosing materials for specific industrial environments, engineers consider factors such as:
- Operating temperature range
- Exposure to corrosive substances
- Required fatigue life
- Magnetic properties (if relevant)
- Weight limits
- Cost-effectiveness
The table below compares key properties of common spring materials used in spring manufacture.
Material |
Rust Resistance |
Fatigue Life |
Relative Cost |
Stainless Steel |
Excellent |
Good |
Moderate |
High-Carbon Steel |
Poor |
Very Good |
Low |
Nickel coil spring |
Excellent |
Excellent |
High |
Beryllium Copper |
Good |
Good |
Very High |
As distributors and suppliers look at product options, understanding these material properties becomes key for meeting varied client needs. By carefully matching material traits to specific application requirements, engineers can ensure optimal spring performance and longevity across many industries and environments. The right material choice affects everything from a spring’s lifespan to its ability to handle tough conditions, making it a critical factor in successful spring design and use.
Customization Vs Stock Options
When selecting springs, engineers must weigh customization against ready-made options. This choice impacts project outcomes, balancing specific needs with time and budget limits. Several factors determine if custom or stock solutions are best for clients.
Custom-made springs offer exact tailoring to application needs, ensuring top performance in unique or demanding settings. Benefits include:
- Precise dimensional specifications
- Tailored force and deflection traits
- Materials suited to specific operating conditions
- Potential for innovative designs solving complex issues in spring manufacture is vast.
However, custom solutions often have longer lead times and higher initial costs. They’re typically suggested when:
- Standard springs can’t meet performance needs
- The application has unusual size or shape limits
- Special materials are needed for extreme conditions
- Large-scale production can offset higher setup costs
Stock options offer quick availability and cost-effectiveness for common uses. Advantages include coil compression spring designs that enhance performance.
- Shorter lead times, often with same-day shipping
- Lower costs due to mass production
- Known performance data and reliability are crucial for selecting the right type of spring.
- Easy replacement and maintenance
Stock springs are ideal when:
- The application fits standard parameters
- Fast turnaround is crucial
- Budget is tight
- Small quantities are needed
To guide clients effectively, consider these factors:
- Performance needs: How critical are exact specs?
- Timeline: Is there flex in the project schedule?
- Budget: Can the project absorb custom tooling costs?
- Quantity: Will volume justify custom production?
- Long-term needs: Is this a one-time or ongoing requirement?
A mixed approach may sometimes work best, using stock springs for prototypes or low-volume production, then switching to custom solutions as demand grows. This method can balance quick market entry with long-term performance and cost-effectiveness.
In the end, choosing between custom and stock options needs careful review of project details. By fully assessing these factors, engineers can suggest the best spring solution, ensuring top performance, timely delivery, and cost-efficiency for their clients’ industrial uses. The spring design process involves considering various aspects such as coil spring design, compression spring specifications, and torsion spring requirements to find the optimal solution for each unique application.
Leveraging Advanced Design Tools
Modern software and technologies have transformed spring engineering, particularly in the realm of mechanical components. Computer-aided design (CAD) programs and simulation platforms have changed how engineers develop springs, enabling the creation of highly accurate digital models.
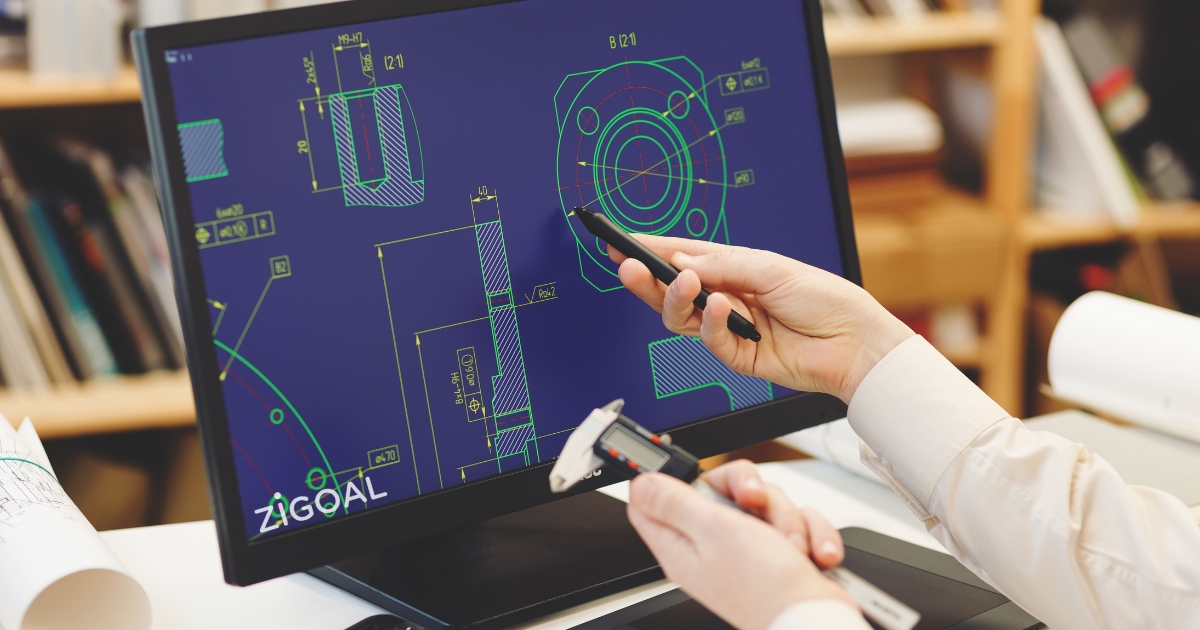
CAD software allows engineers to make exact adjustments to component parameters, ensuring products meet stringent specifications. The ability to fine-tune dimensions, force requirements, and other critical factors with unprecedented accuracy has significantly improved spring design outcomes. These tools enable precise simulation of how products will perform under various conditions.
Simulation tools provide virtual testing environments, reducing the need for physical prototypes. This capability speeds up the design process, allowing engineers to iterate quickly. By simulating a spring’s behavior under different loads and environmental conditions, potential issues can be identified and resolved before production begins.
Advanced design tools have become essential in addressing the evolving needs of various sectors. The precision offered by these technologies allows engineers to meet exacting tolerances and performance requirements across a wide range of industries, from aerospace to medical devices. The coil spring design process has been greatly enhanced by these tools.
The ability to rapidly prototype and test designs virtually has shortened development cycles. This efficiency is crucial in today’s fast-paced industrial landscape, where time-to-market can be a critical factor in a product’s success. Engineers can now explore complex geometries and novel materials that were previously impractical to test or manufacture, leading to breakthroughs in spring performance and longevity.
Key Advancements in Engineering Design
- CAD software enables the creation of highly accurate digital models, allowing for precise dimensional control and optimization of spring geometry
- Simulation platforms reduce the need for physical prototypes, cutting development time and costs
- Virtual testing environments can simulate product behavior under various conditions, including extreme temperatures, corrosive environments, and high-stress scenarios
- Advanced visualization options enhance productivity in finding and comparing spring applications across industries, particularly in coil compression designs.
- Integration of material databases with design tools allows for rapid assessment of different alloys and their impact on spring performance
As the industry continues to evolve, the integration of artificial intelligence and machine learning with these design tools promises to further revolutionize the field, potentially automating aspects of the design process and offering predictive insights into long-term spring behavior. These advancements are crucial for engineers working with compression springs, torsion springs, and other types of coil springs.
What are the main types of coil springs available for design options?
The three main types of coil springs are compression springs, extension springs, and torsion springs. Each type serves different applications and has unique design considerations.
How can I use a compression spring finder to select the right spring?
A compression spring finder allows you to quickly search for springs based on specific parameters such as diameter, material, and force requirements.
What is involved in the coil spring design process?
The coil spring design process involves considering factors such as load requirements, material selection, and the intended application. Additionally, using a spring calculator can help optimize dimensions and performance for your specific needs.
Can I customize my coil spring, and how do I initiate this process?
Yes, you can create custom compression springs to meet your particular spring specification. To initiate the process, feel free to
contact our sales teams for help on design or finding the right spring based on your requirements.
What should I consider when selecting a stock extension spring?
When selecting a stock extension spring, consider the required load, length, and the environment in which the spring will operate. These factors will influence the performance and longevity of the spring in your application.
How do I calculate the specifications for a custom spring?
You can use a spring calculator to determine the specifications for a custom spring. This calculator will take into account factors such as wire diameter, coil diameter, and number of active coils to ensure that the spring meets your design requirements.
What applications commonly use coil springs?
Coil springs are widely used in various applications, including automotive, aerospace, industrial machinery, and consumer goods. Their versatility allows them to be utilized in scenarios requiring energy storage, movement control, and load support.